Variable Speed Fan Controls
alternative practice names:
Fan Variable Speed Drive (VSD); Fan Variable Frequency Drive (VFD); Fan Controls; Ventilation VFD/VSD; Fan Controller
Variable speed fan controls, commonly called a fan VFD or simply fan controls, can significantly reduce dairy fan electricity usage by automatically varying the speed of fans based on the ambient temperature and humidity. Savings is achieved by running fans at lower speeds when maximum airflow from the fans isn’t needed to provide adequate cow cooling.
Fan controls consist of two main components: a variable speed drive (VSD, also known as a VFD), and environmental sensors. Some fan control products integrate the VFD and control software into the same product, whereas other products consist of a third-party controller and environmental sensors that connect to fan VSDs to modulate the fan speed; some of these products also allow for automated operation of barn curtains and other equipment.
The most advanced fan control systems come with smart phone and web applications to allow the dairy operator to remotely monitor fan operating metrics. High efficiency fans that use electronically commutated (EC) motors effectively have a built-in VFD and do not require an add-on VFD to control the motor speed, they just need a third-party solution to control the fan speed using environmental sensors.
When used, in what regions in the U.S. is the practice found:
Northwest, West, Upper Midwest, Southwest, Northeast, Southeast
FARM SIZE
When used, typically found on farms of the following sizes:
All Sizes

Practice Benefits
Increased profitability: The main benefit of installing variable speed fan controls is a reduction in electricity costs. Furthermore, because VFDs reduce the average motor speed of fans, they may extend the lifespan of fan motors and reduce maintenance costs.
Increased labor efficiency: Reduced labor costs may be an additional benefit on dairy farms that manually turn fans on and off based on temperature. Advanced fan control systems with mobile applications can also provide additional insight and operational data to dairy farm operators.
We're always eager to update the website with the latest research, implementation insights, financial case studies, and emerging practices. Use the link above to share your insights.

Implementation Insights
Site-specific or Farm-specific requirements
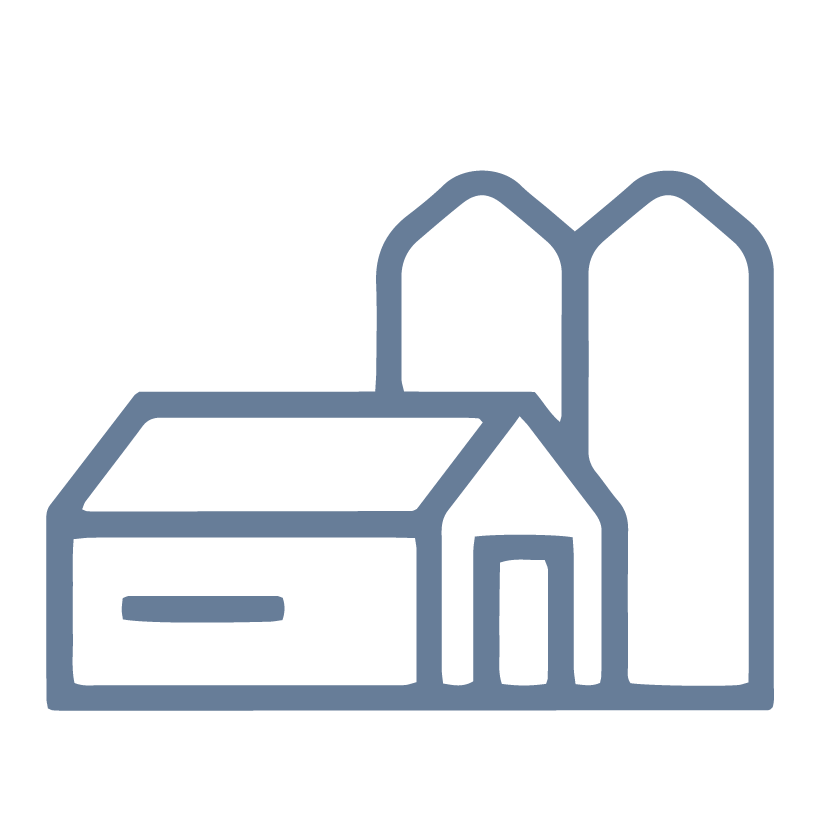
Operational compatibility: Ventilation requirements in dairy barns vary considerably by location and barn style, so it is important to consult with a dairy ventilation expert to determine what type of fan controls are most suitable for a specific barn. Variable speed fan controls are widely applicable and there are usually solutions available to retrofit existing fans, although sometimes the most energy-efficient option is to install new high-efficiency fans equipped with EC motors at the same time as installing variable speed controls.
Required Capital Expenditures (CapEx)
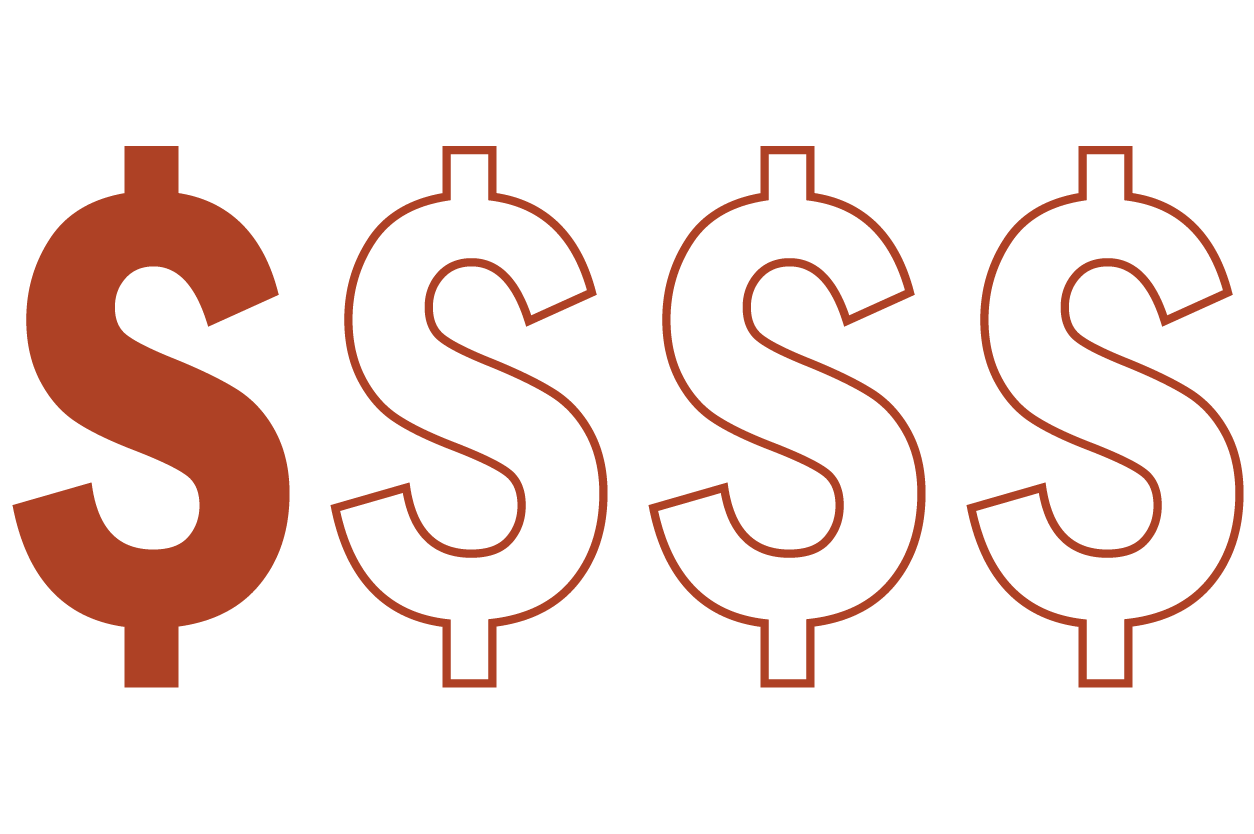
Variable speed fan control system: The primary expense is the variable speed fan control system itself along with the labor required to install it. If existing fans are compatible with VFDs, a single VFD can be purchased and installed to control each individual fan, or a larger VFD can be installed to control an array of fans. An equipment vendor with experience in designing and installing dairy barn ventilation systems should always be consulted when considering the installation of a ventilation variable speed control system to ensure that it is correctly calibrated and programmed for local conditions.
Required Operational Expenditures (OpEx)
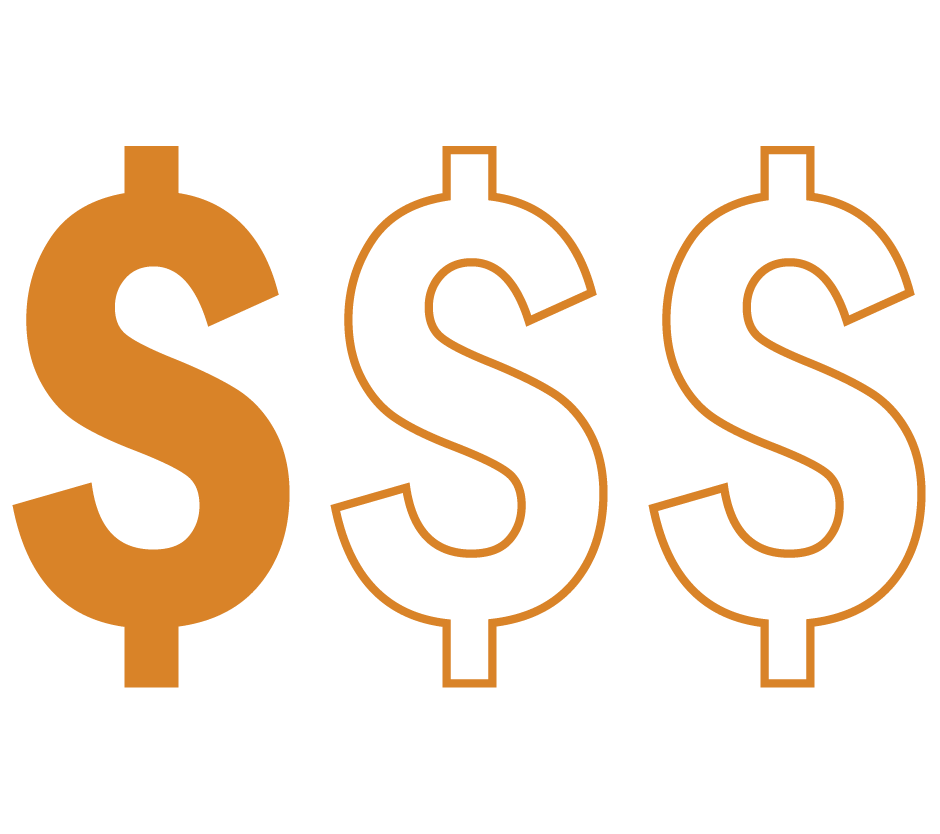
Maintenance: Ongoing maintenance costs for variable speed fan controllers are generally low. The electricity cost savings realized from installing variable speed fan controls will greatly outweigh any ongoing maintenance costs. Variable speed fan controls generally have a long useful life and should last at least 10 to 20 years. Fan controllers and the VFDs they control are usually built to operate in dusty conditions and are sealed to prevent damage from water. Assistance from the equipment vendor may be needed to recalibrate temperature sensors occasionally, or to reprogram setpoints of the fan controller as needed.
Implementation Considerations
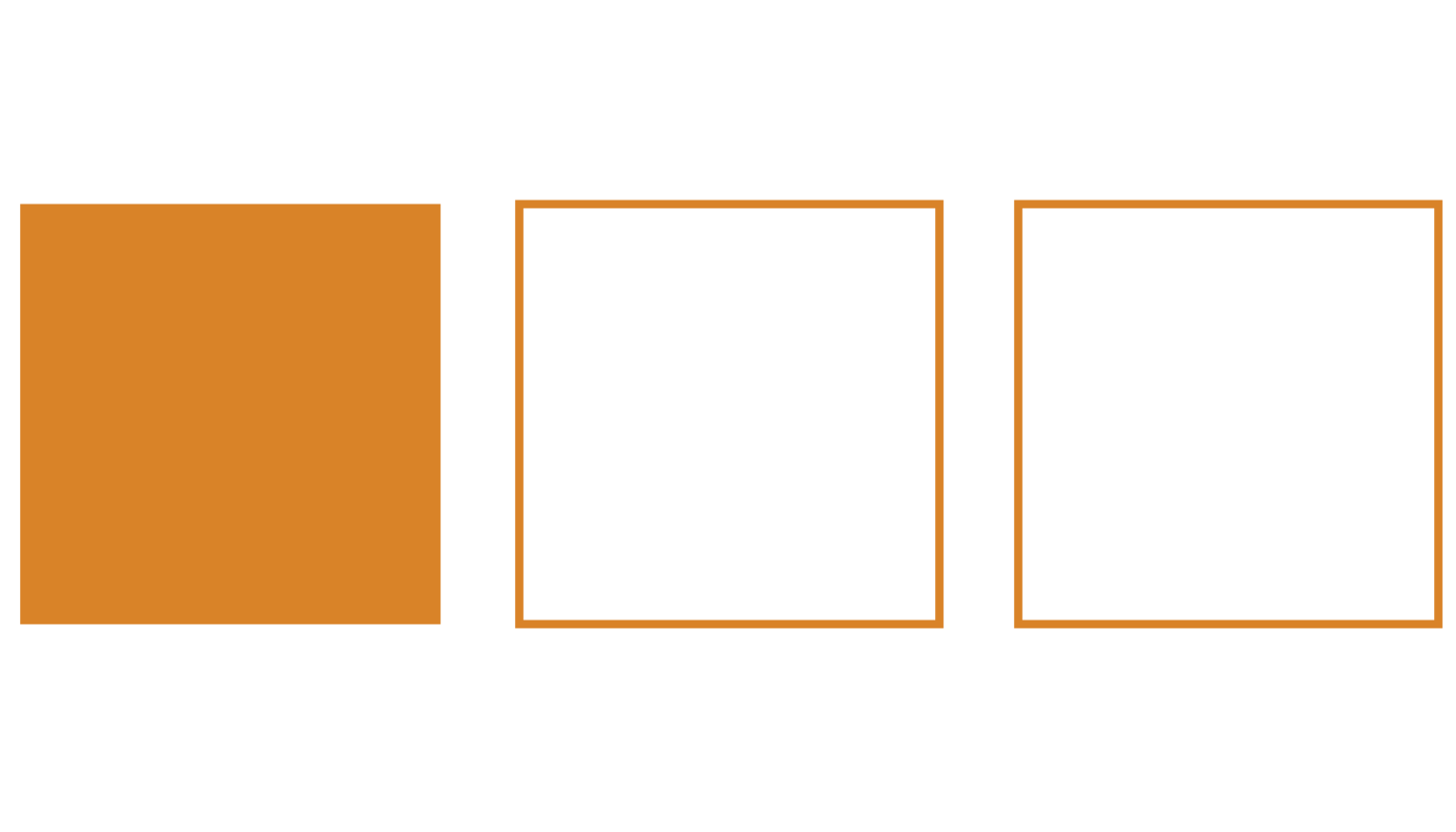
Selection and installation: Variable speed fan controls are generally straightforward to install with the design and installation assistance of an experienced equipment vendor and electrician. It is important to select high-quality VFDs with radiofrequency filters to avoid electrical interference with other equipment on the farm. When properly designed and installed, fan controls should operate seamlessly with minimal need for maintenance and adjustment. Purchasing a fan control system from a reputable vendor that includes a warranty will help to ensure seamless integration with the ventilation system.
Financial Considerations and Revenue Streams
FEDERAL COST-SHARE AND CONSERVATION FUNDING
Funding is available for this practice through USDA's Natural Resources Conservation Service (NRCS) Environmental Quality Incentives Program (EQIP) On-Farm Energy Initiative.
Related EQIP Practice Standard: Energy Efficient Agricultural Operation (374).
Notes:
An Agricultural Energy Management Plan (AgEMP), or other qualifying energy audit, needs to be completed before applying for EQIP assistance.
Check with the local NRCS office on payment rates and practice requirements relevant to your location.
The USDA Rural Development Rural Energy for America Program (REAP) also offers competitive grants and loan guarantees for installing energy efficiency projects.
OTHER CONSERVATION FUNDING
Incentives and rebates for variable speed fan controls are sometimes available through the farm’s electric utility company. Utility rebate programs usually pay rebates based on the motor horsepower of the fans being controlled (e.g., $100-$200 per horsepower).
Additional Resources
Article: Variable speed drives in the dairy shed (Pump Industry)
Book: Dairy Farm Energy Efficiency (ATTRA)
Presentation: Farm Energy IQ (Penn State Extension)
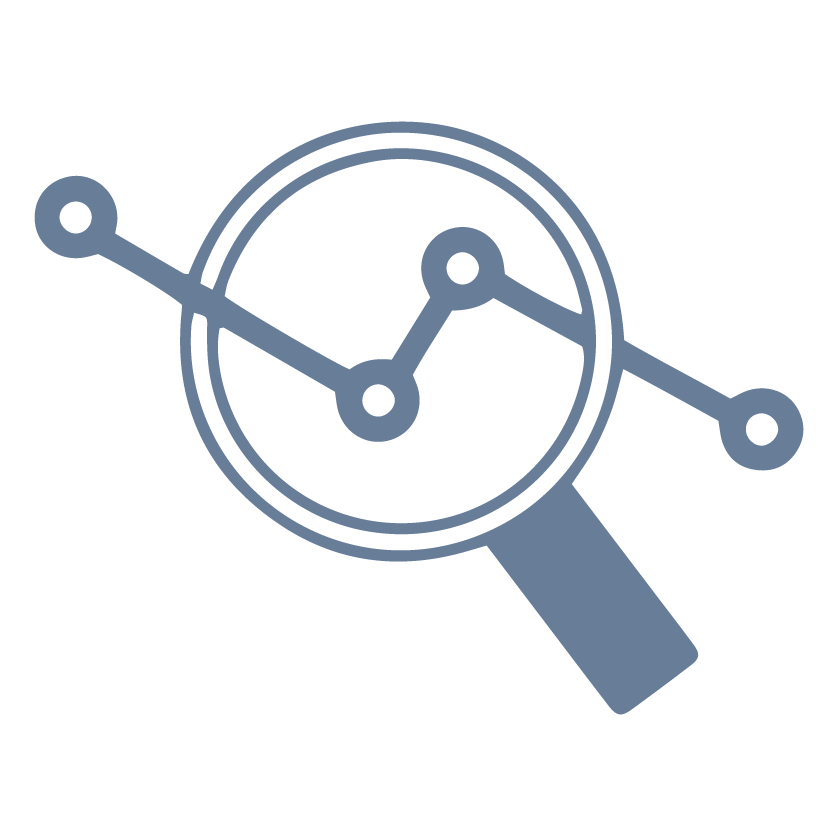
Environmental Impacts
REDUCES FARM GREENHOUSE GAS FOOTPRINT
Improving energy use efficiency reduces a farm's greenhouse gas (GHG) footprint. Since energy production typically involves processes that emit greenhouse gases like carbon dioxide and methane, cutting energy use directly lowers the GHG footprint of the farm.
Contents
We're always eager to update the website with the latest research, implementation insights, financial case studies, and emerging practices. Use the link above to share your insights.
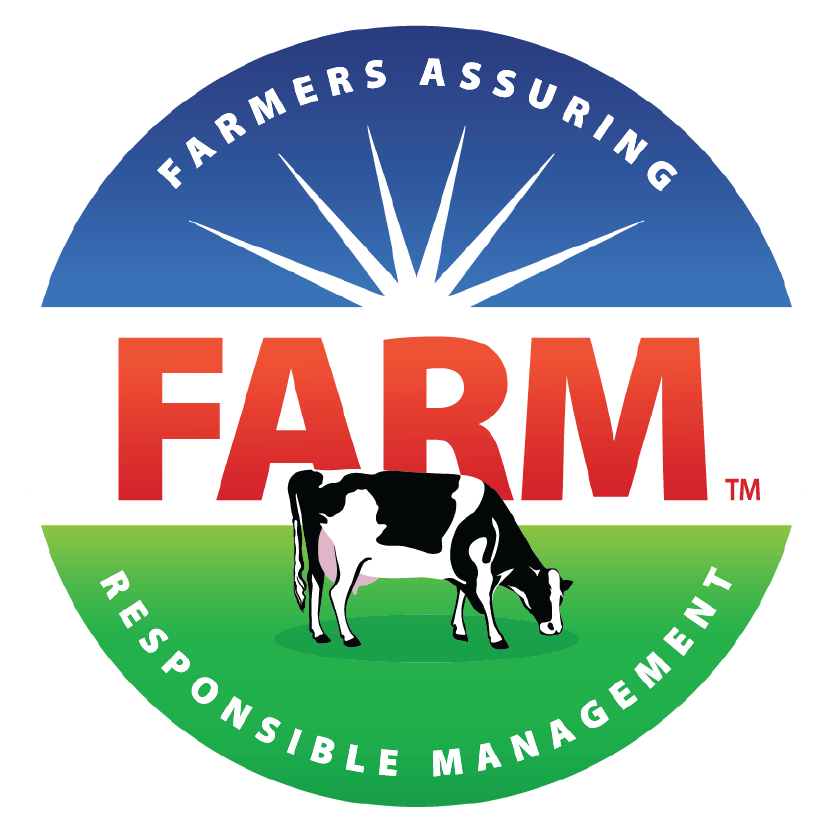
Alignment with FARM Program
FARM Environmental Stewardship (ES) V2-V3 Alignment
FARM ES captures a farm's energy usage and calculates the associated GHG emissions based on regional energy production and transmission averages. Any practice that reduces farm energy consumption will directly lower the farm's GHG footprint. The reduction in GHG emissions is particularly pronounced in regions where a larger proportion of energy is derived from coal, natural gas, or other fossil fuel sources, as these energy types have higher carbon footprints compared to renewable energy sources.
Variable speed fan controls, commonly called a fan VFD or simply fan controls, can significantly reduce dairy fan electricity usage by automatically varying the speed of fans based on the ambient temperature and humidity. Savings is achieved by running fans at lower speeds when maximum airflow from the fans isn’t needed to provide adequate cow cooling.
Fan controls consist of two main components: a variable speed drive (VSD, also known as a VFD), and environmental sensors. Some fan control products integrate the VFD and control software into the same product, whereas other products consist of a third-party controller and environmental sensors that connect to fan VSDs to modulate the fan speed; some of these products also allow for automated operation of barn curtains and other equipment.
The most advanced fan control systems come with smart phone and web applications to allow the dairy operator to remotely monitor fan operating metrics. High efficiency fans that use electronically commutated (EC) motors effectively have a built-in VFD and do not require an add-on VFD to control the motor speed, they just need a third-party solution to control the fan speed using environmental sensors.
Practices and technologies
Variable Speed Fan Controls
alternative practice name:
Fan Variable Speed Drive (VSD); Fan Variable Frequency Drive (VFD); Fan Controls; Ventilation VFD/VSD; Fan Controller
REGIONALITY
When used, in what regions in the U.S. is the practice found:
Northwest, West, Upper Midwest, Southwest, Northeast, Southeast
COMPARABLE FARM SIZE
When used, typically found on farms of the following sizes:
0 - 100 cows, 100 - 500 cows, 500 - 2500 cows, 2500 - 5000 cows, Over 5000 cows

Practice Benefits
Increased profitability: The main benefit of installing variable speed fan controls is a reduction in electricity costs. Furthermore, because VFDs reduce the average motor speed of fans, they may extend the lifespan of fan motors and reduce maintenance costs.
Increased labor efficiency: Reduced labor costs may be an additional benefit on dairy farms that manually turn fans on and off based on temperature. Advanced fan control systems with mobile applications can also provide additional insight and operational data to dairy farm operators.

Implementation Insights
Site-specific or Farm-specific requirements
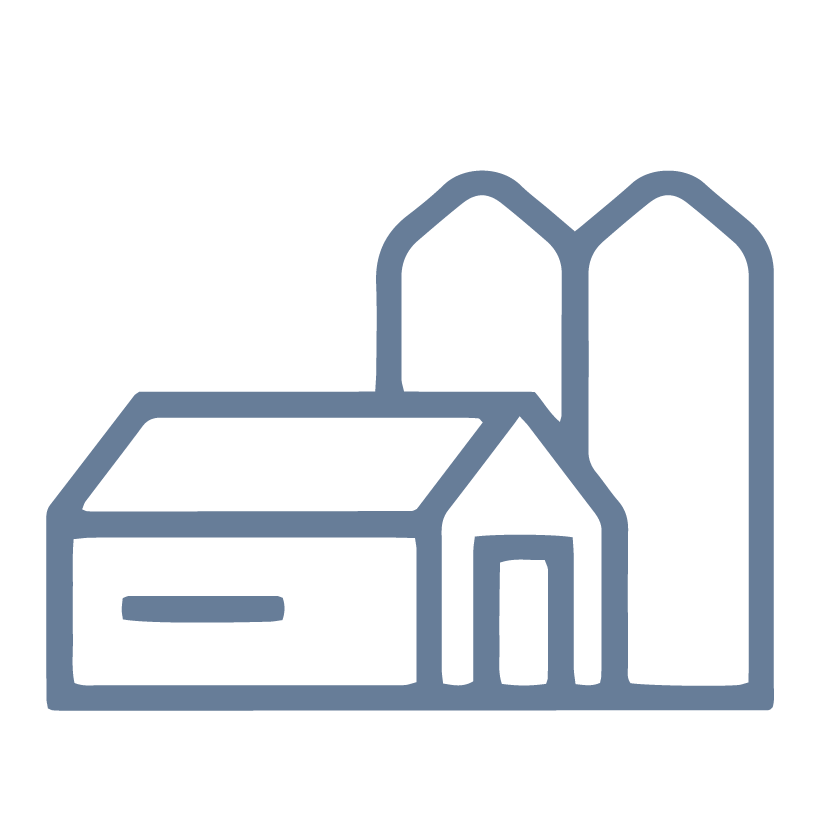
Operational compatibility: Ventilation requirements in dairy barns vary considerably by location and barn style, so it is important to consult with a dairy ventilation expert to determine what type of fan controls are most suitable for a specific barn. Variable speed fan controls are widely applicable and there are usually solutions available to retrofit existing fans, although sometimes the most energy-efficient option is to install new high-efficiency fans equipped with EC motors at the same time as installing variable speed controls.
Required Capital Expenditures (CapEx)
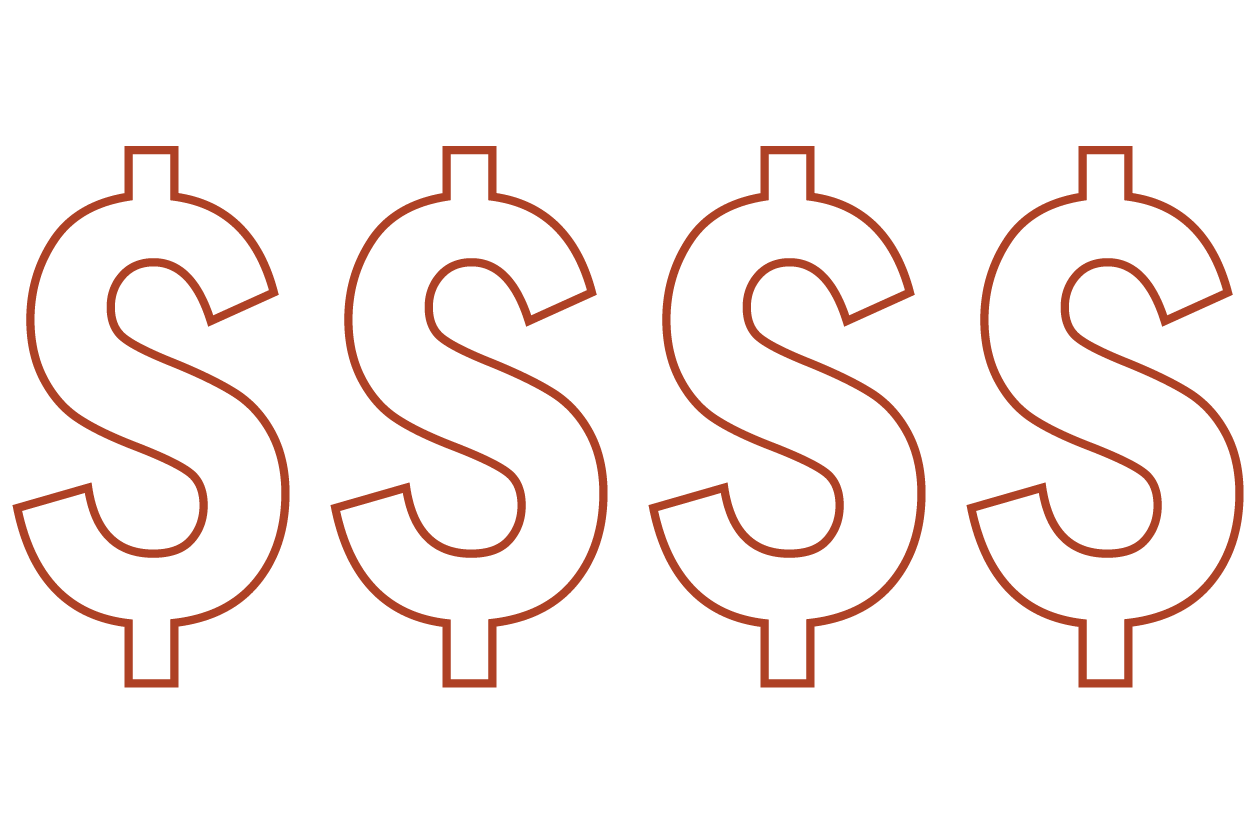
Variable speed fan control system: The primary expense is the variable speed fan control system itself along with the labor required to install it. If existing fans are compatible with VFDs, a single VFD can be purchased and installed to control each individual fan, or a larger VFD can be installed to control an array of fans. An equipment vendor with experience in designing and installing dairy barn ventilation systems should always be consulted when considering the installation of a ventilation variable speed control system to ensure that it is correctly calibrated and programmed for local conditions.
Required Operational Expenditures (OpEx)
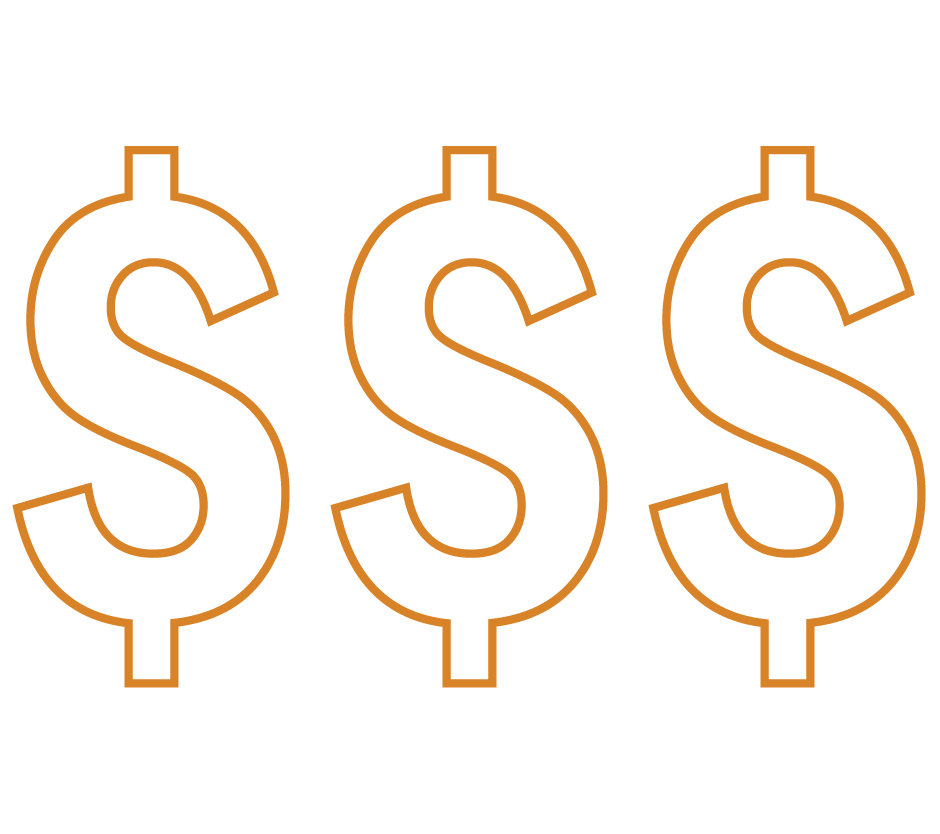
Maintenance: Ongoing maintenance costs for variable speed fan controllers are generally low. The electricity cost savings realized from installing variable speed fan controls will greatly outweigh any ongoing maintenance costs. Variable speed fan controls generally have a long useful life and should last at least 10 to 20 years. Fan controllers and the VFDs they control are usually built to operate in dusty conditions and are sealed to prevent damage from water. Assistance from the equipment vendor may be needed to recalibrate temperature sensors occasionally, or to reprogram setpoints of the fan controller as needed.
Implementation Considerations
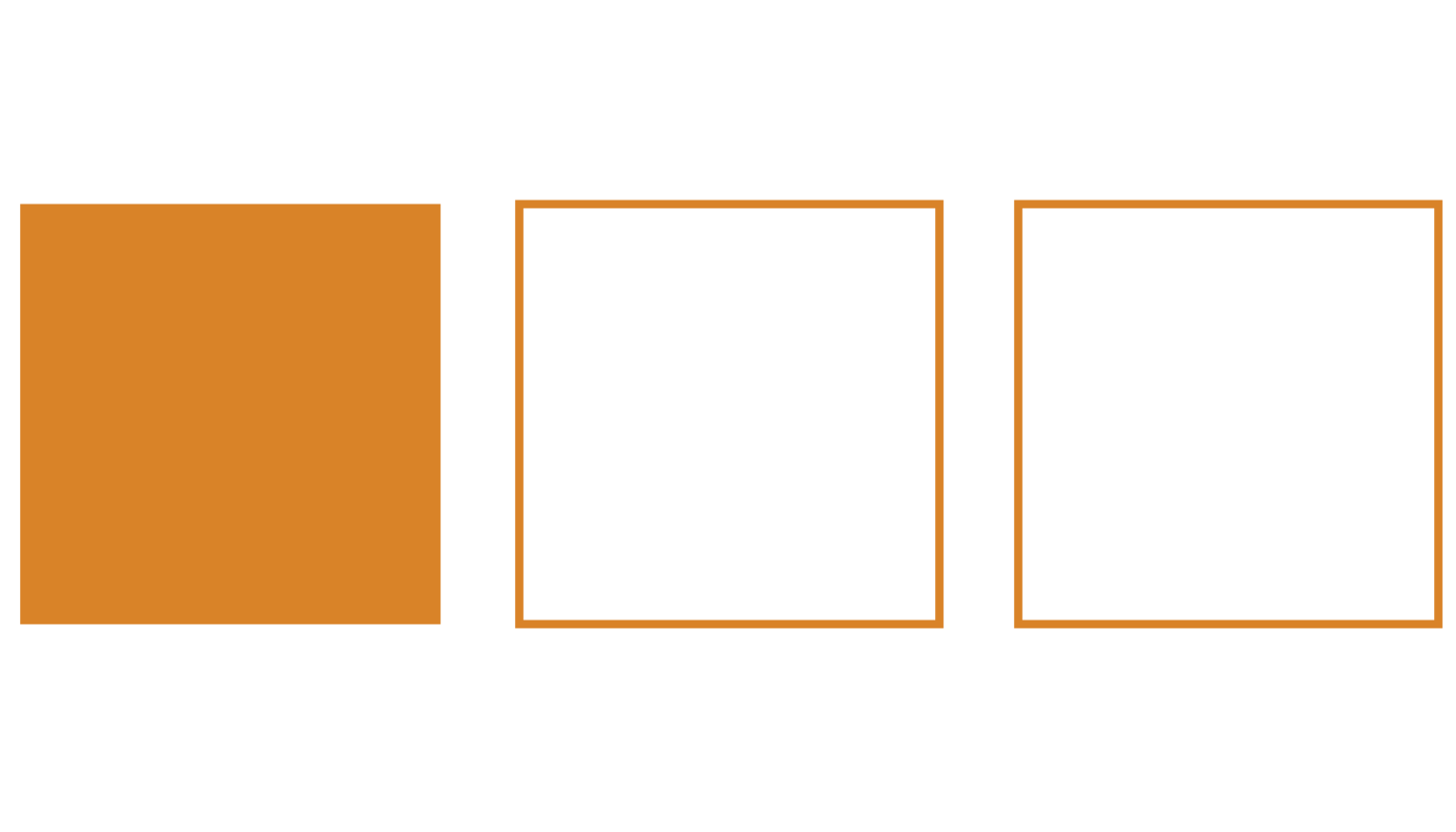
Selection and installation: Variable speed fan controls are generally straightforward to install with the design and installation assistance of an experienced equipment vendor and electrician. It is important to select high-quality VFDs with radiofrequency filters to avoid electrical interference with other equipment on the farm. When properly designed and installed, fan controls should operate seamlessly with minimal need for maintenance and adjustment. Purchasing a fan control system from a reputable vendor that includes a warranty will help to ensure seamless integration with the ventilation system.
Financial Considerations and Revenue Streams
FEDERAL COST-SHARE AND CONSERVATION FUNDING
Funding is available for this practice through USDA's Natural Resources Conservation Service (NRCS) Environmental Quality Incentives Program (EQIP) On-Farm Energy Initiative.
Related EQIP Practice Standard: Energy Efficient Agricultural Operation (374).
Notes:
An Agricultural Energy Management Plan (AgEMP), or other qualifying energy audit, needs to be completed before applying for EQIP assistance.
Check with the local NRCS office on payment rates and practice requirements relevant to your location.
The USDA Rural Development Rural Energy for America Program (REAP) also offers competitive grants and loan guarantees for installing energy efficiency projects.
OTHER CONSERVATION FUNDING
Incentives and rebates for variable speed fan controls are sometimes available through the farm’s electric utility company. Utility rebate programs usually pay rebates based on the motor horsepower of the fans being controlled (e.g., $100-$200 per horsepower).
Additional Resources
Article: Variable speed drives in the dairy shed (Pump Industry)
Book: Dairy Farm Energy Efficiency (ATTRA)
Presentation: Farm Energy IQ (Penn State Extension)
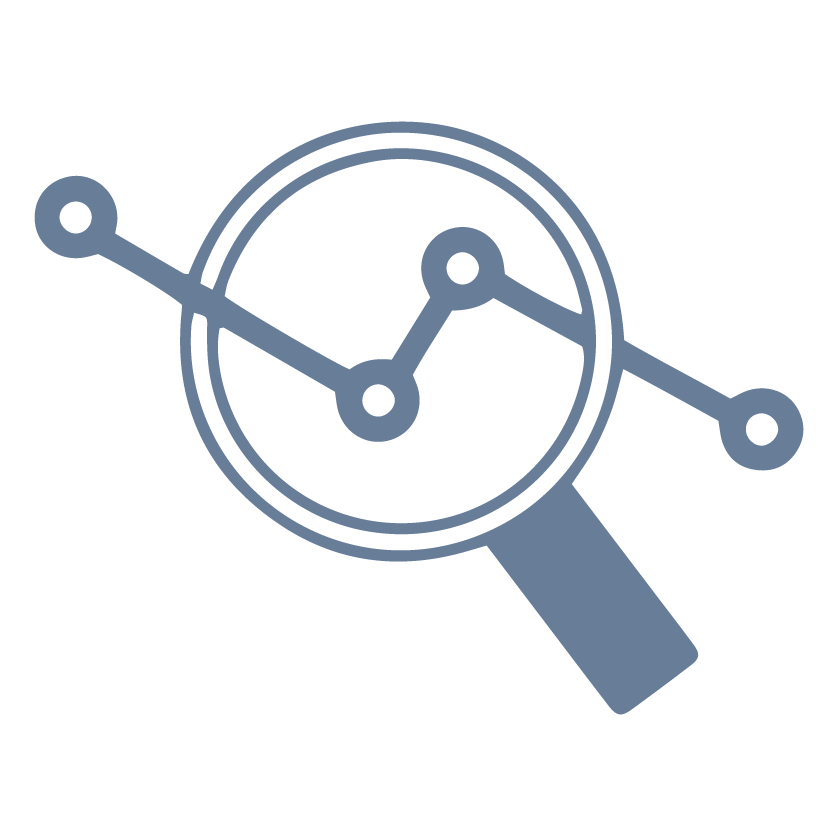
Research
REFerences
REDUCES FARM GREENHOUSE GAS FOOTPRINT
Improving energy use efficiency reduces a farm's greenhouse gas (GHG) footprint. Since energy production typically involves processes that emit greenhouse gases like carbon dioxide and methane, cutting energy use directly lowers the GHG footprint of the farm.
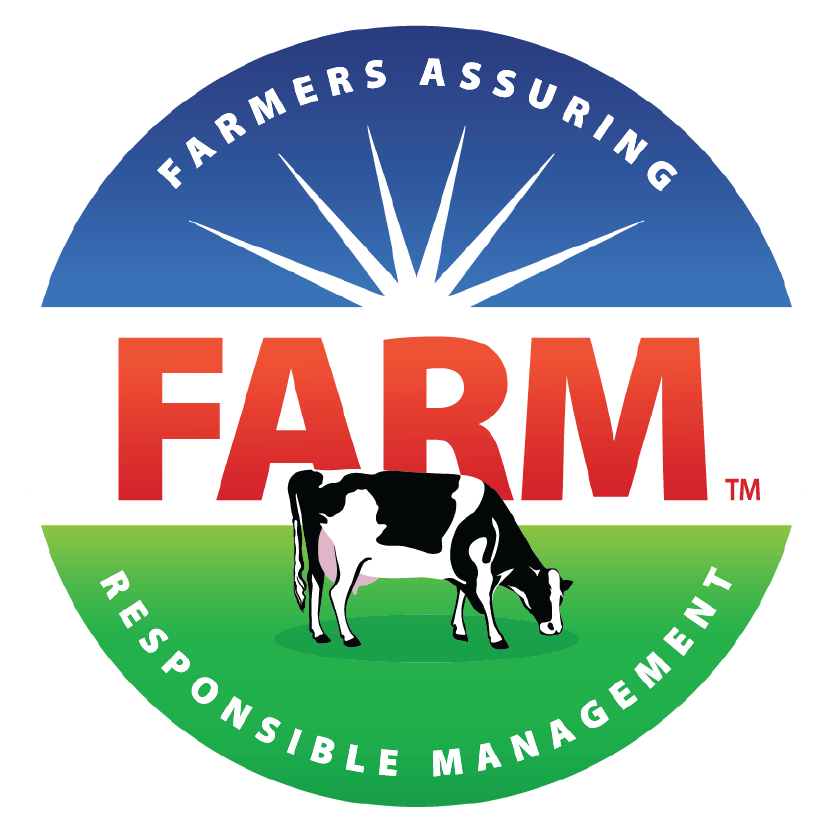
Alignment with FARM Program
FARM Environmental Stewardship (ES) V2-V3 Alignment
FARM ES captures a farm's energy usage and calculates the associated GHG emissions based on regional energy production and transmission averages. Any practice that reduces farm energy consumption will directly lower the farm's GHG footprint. The reduction in GHG emissions is particularly pronounced in regions where a larger proportion of energy is derived from coal, natural gas, or other fossil fuel sources, as these energy types have higher carbon footprints compared to renewable energy sources.